
Precise locking system, outstanding efficiency, efficient servo drive, all meet all requirements. Focus on customer products, provide a complete set of technical solutions for customers, and create better investiment returns and customer experience for global customers.
Mold opening & closing with 4 stages control, ejecting with 2 stages control. Clamping and ejection are by liner potentionmeter. Its precision can reach 0.01mm, and control the clam-ping and ejection stroke route accurately. Ejector have function of vibration ejection, ejection atop, multiple ejection pressure and speed of ejection can piecewise set by computer Equippde with high precision low pressure mold closing protection it can be set directly by monitor, low pressure result is perfect. Toggle is used by auto lubrication system, lubrication steeing can be operated monitored on the panel directly. And it owns lubrication failure, to machine normal operation.
A hydraulic motor drives a planetary gear to ensure perfect and rigid mold height adjustment.
Optimized template design, improve the rigidity and precision of mold open/closing.
Increase the speed and saves power from 20%~50% depending upon the molding.
MOLD CLAMPING UNIT
High Precision
High rigidity
High response
Improved the precision of the machine and prolong the service life of the machine greatly reduced the consumption!
In view of different material and applications we supply variety of screw and barrel for customer choice.
Injection unit adopts linear guide rail built-in carriage cylinder, and integral casting support, thus enhence its rigidity, and make the compact structure.
Double-carriage cylinder is adopted to ensure stable injection.
INJECTION NUIT
High precision
High stability
The controller is adopting 400M high speed CPU, which can equip with semi-closure of fully closed system. Plus personality graphic operation interface, curve online testing function and central network connetion management. Ample SPC quality management interface, it is absolutely the best tool to make profit.
Equippde with six stages injection, three stages holding pressure, twostages suck back and the holding pressure posittion switching controls etc, can flexibly adust according to different products. Precise injectionend and holding pressure positon switching practice high precision andhigh stability injection function adopt lineal electrical ruler, precisionreaches 0.01mm, which can accurately control injection strok. it canrecord and display simultaneously samping temperature curve during continuous production process, injection and holding pressure switchingpoint and holding pressure finishing point. Having the function of historical curve allocation, its precision can reach 0.1mm, and system stability is visibleSix PID stages barrel temperature control is precision can reach. it also has temperature abnormal & electrical wore disconnertion alarmfunction, which is able to control the barrel temp-erature accurately. Screwlow temperature staring protection ( cold start ) can be prevent screw from damages accidentally, adjustable pre-heat temperature keeping and barrel auto heating function, which can arbitrarily set cleaning.
CONTROL SYSTEM:
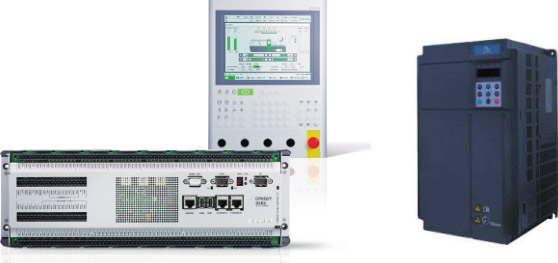
Spsystem consist of variable pump & varialbe speed motor flow (speed) control/ pressure control Servo Motor
COMPARISON OF POWER CONSUMPTION
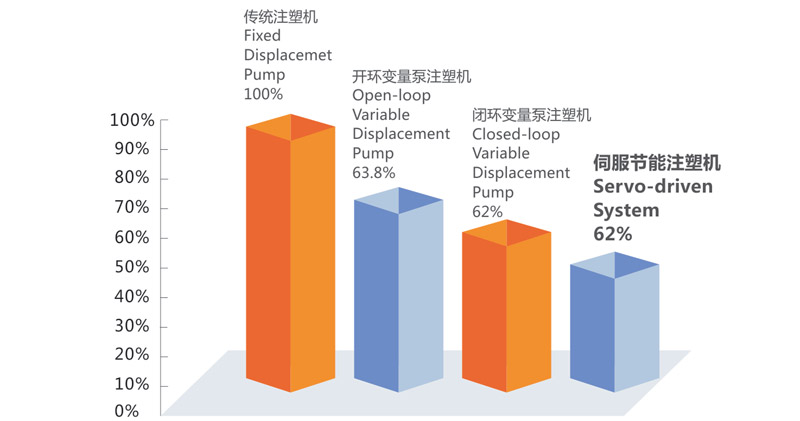
DRIVE TECHNOLOGY
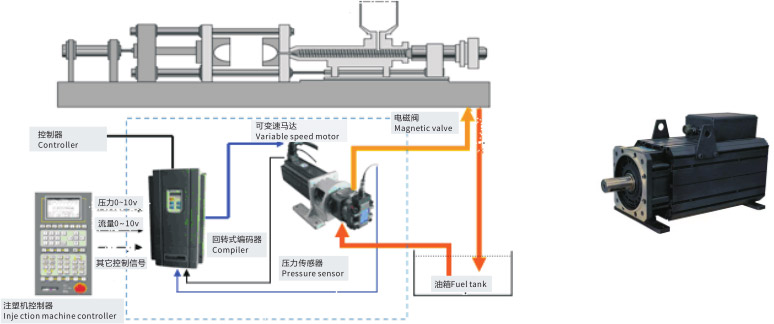
TECHNICAL PARAMETERS
Project | Unit | YS-200 | |||
Injection Unit | Screw diameter | mm | Φ44 | Φ50 | Φ54 |
Theoretical shot weight | cm3 | 342 | 442 | 515 | |
Shot weight of injection (ps) | gram | 305 | 394 | 460 | |
ozs | 10.8 | 13.9 | 16.2 | ||
Injection pressure | kg/cm2 | 2440 | 1890 | 1620 | |
Injection velocity | mm/s | 96 | |||
Injection rate | cm3/sec | 145 | 188 | 219 | |
Clamping Unit | Mould clamping force | metrictons | 200 | ||
Mould clamping stroke | mm | 160-610 | |||
Mould thickness | mm | 332*332 | |||
Min mould thickness | mm | 510*510 | |||
Distance between tie bar | mm | 745*745 | |||
Mould platen (hxv) | mm | 130 | |||
Ejector stroke | mm | 21.2 | |||
Electrical Equipment | Max. Motor power | kw | (0-400C)*5 | ||
Temp controller | (range)set | 14.4 | |||
Heater capacity | kw | 6080*1250*1860 | |||
Others | Dimension | mm | 340 | ||
Machine weight | metric tons | 7.5 | |||
System pressure | kg/cm2 | 140 | |||
Platen dimensions | ![]() | ||||
Platen dimensions | ![]() |
Note: The output of this product parameter is calculated according to the specific gravity of polystyrene of 1.05, assuming an efficiency of 0.88. As the product is continuously researched and improved, the design changes are subject to change without notice.